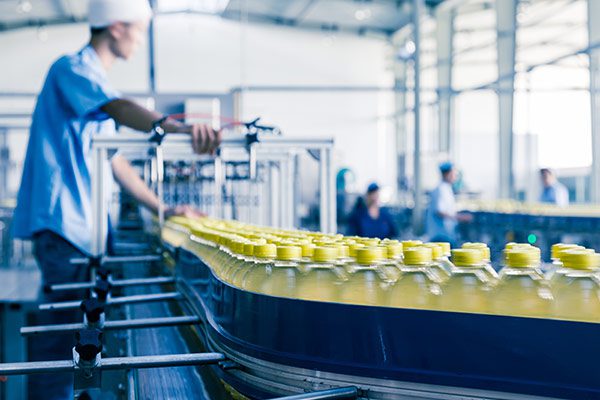
Food and Beverage
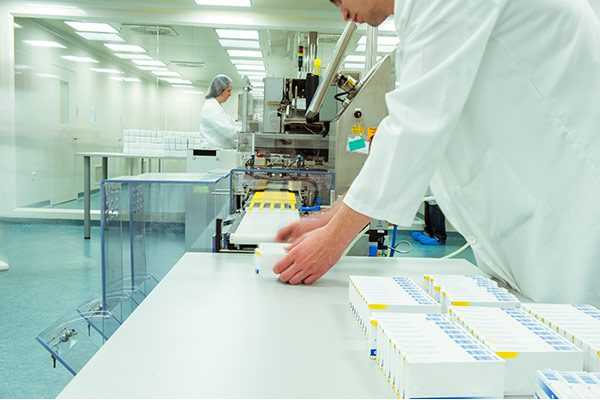
Medical and Pharmaceutical
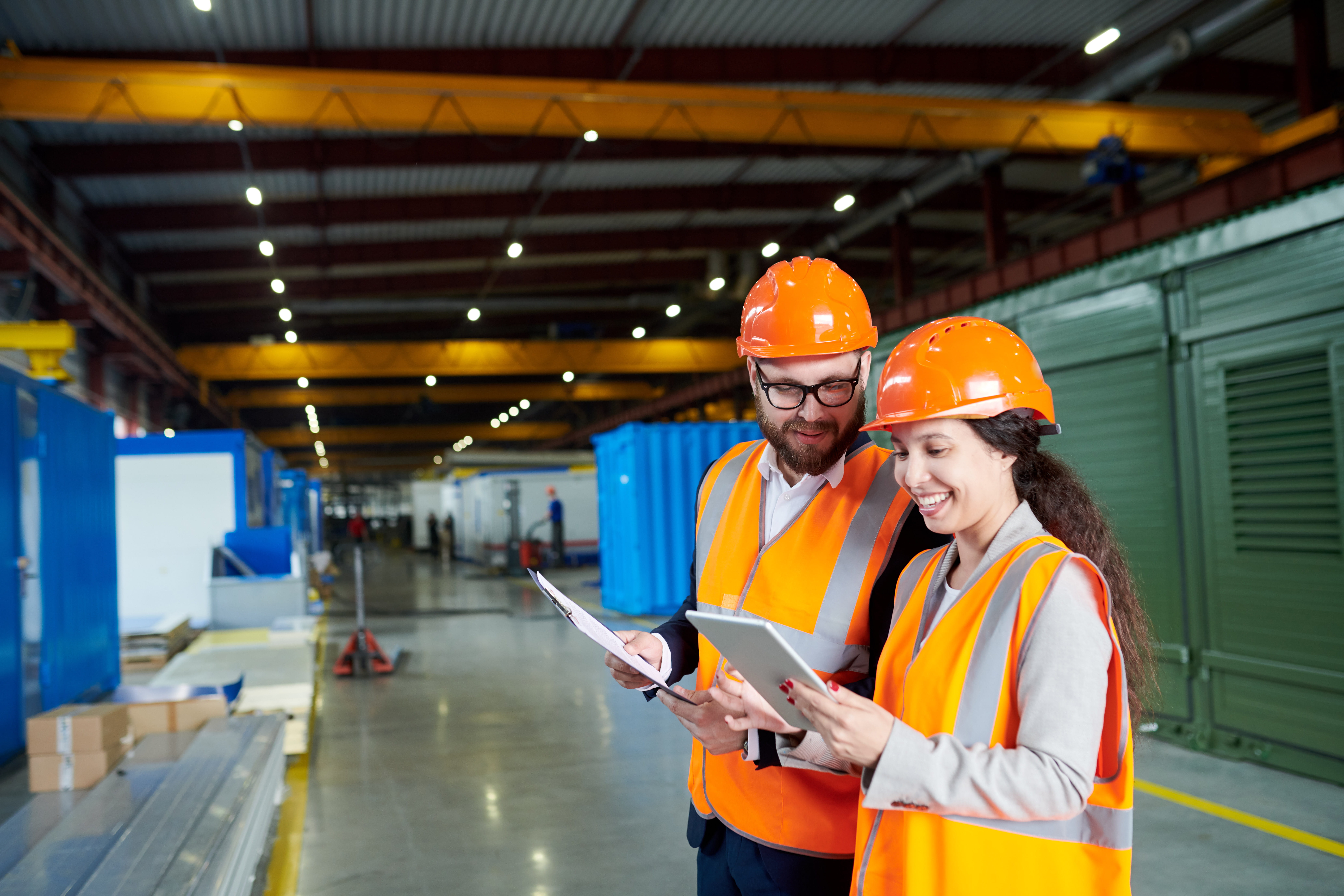
Consumer Packaged Goods
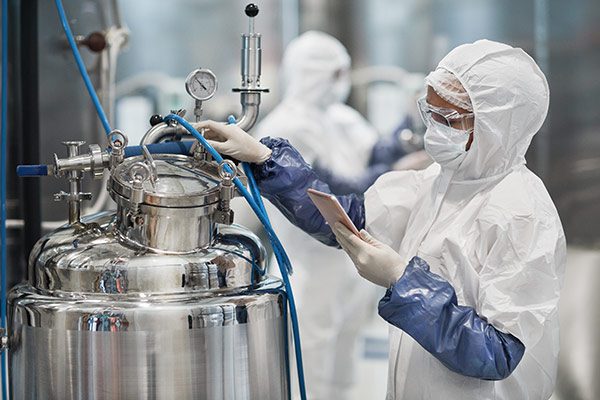
Chemical
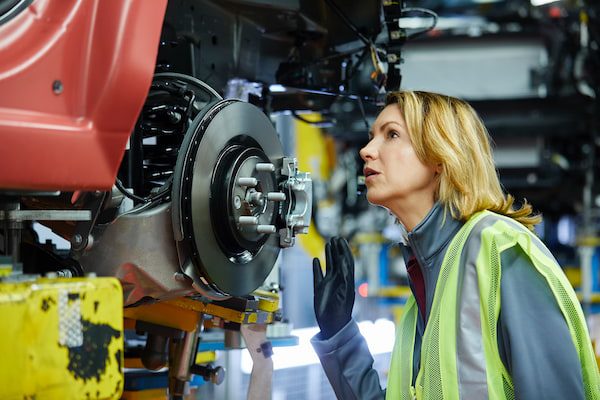
Automobile and Industrial
Trusted by the World’s Most Recognized Brands
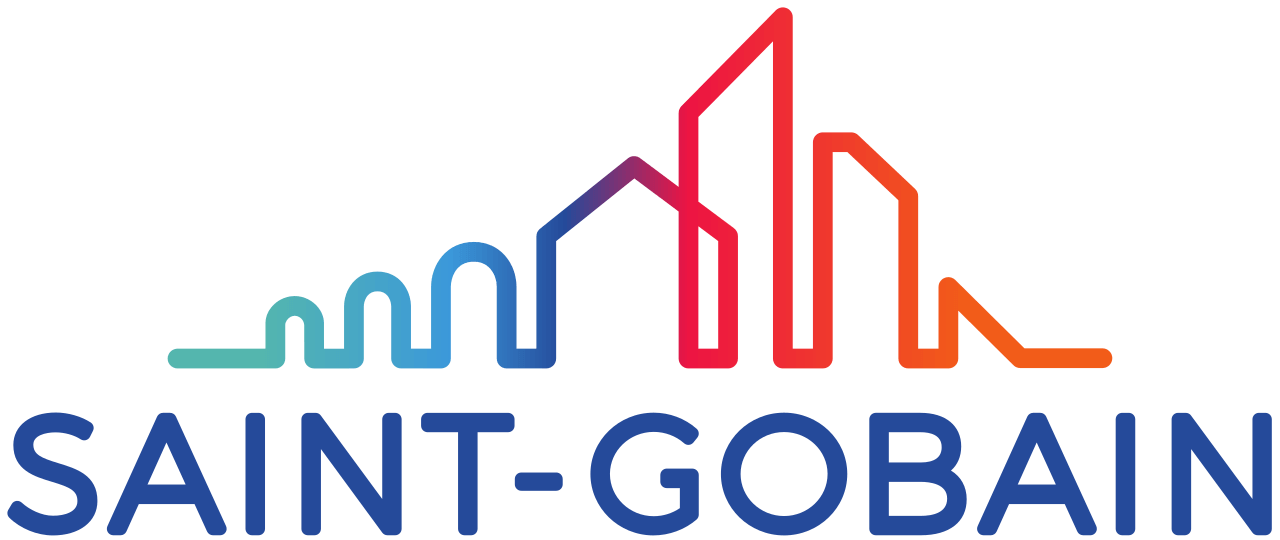
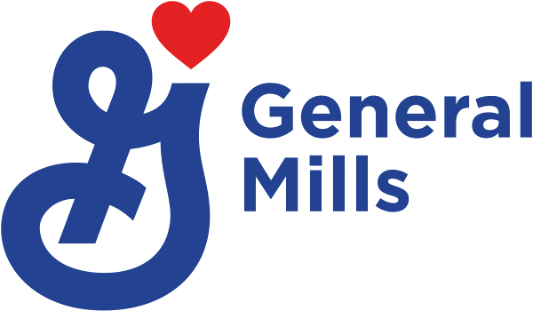

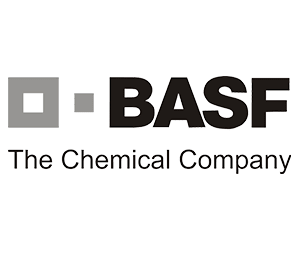

As many as 2.1 million manufacturing jobs will be unfilled through 2030.
87% of hourly workers surveyed want more control over their work schedules.
Scheduling automation can reduce unplanned overtime by up to 41%.
Align Staffing to Production Plans
Create accurate staffing plans to meet product targets.
- Align staffing demand and skill-mix requirements to production plans.
- Create worker schedules to match your production line schedules.
- Identify staffing gaps in advance and mitigate understaffing issues early.
- Build an adequate pool of workers for backup contingency.
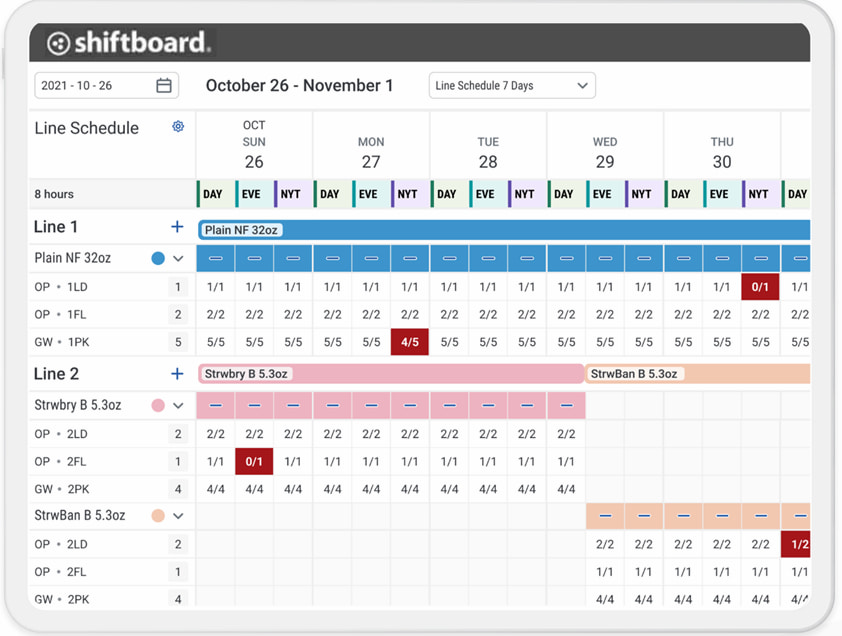
Ensure Smooth Operations
Respond swiftly to call-offs, supply chain disruptions, and other unexpected changes.
- Find coverage quickly with an automatic list of available and qualified workers.
- Assign workers in the order required by plant-specific scheduling procedures.
- Block violations against employment laws, union contracts, and internal policies.
- Notify workers of schedule changes and promote shift openings automatically.
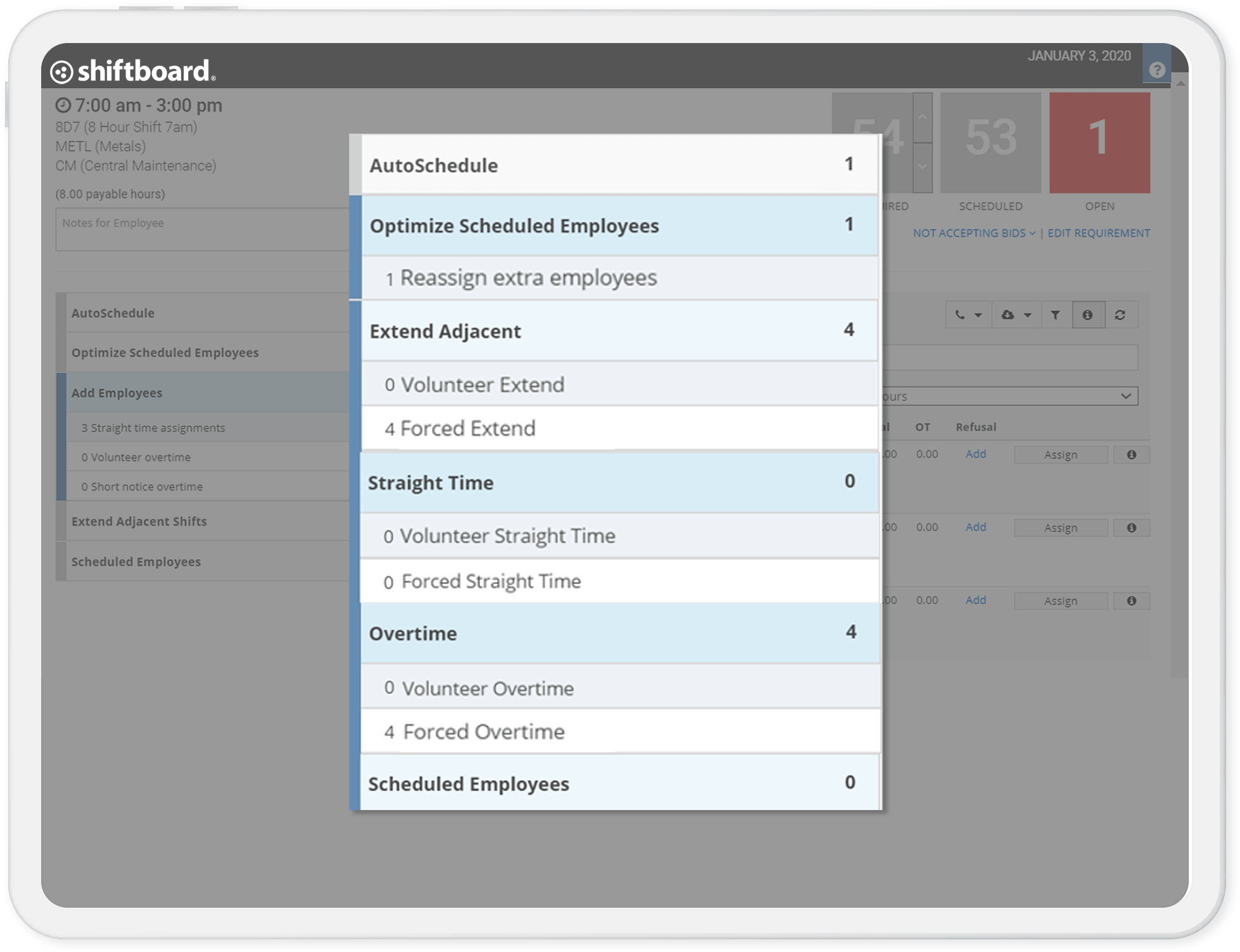
Attract and Retain Workers
Keep workers satisfied and reduce turnover with flexible, transparent, and fair schedules.
- Collect and accommodate worker availability and schedule preferences.
- Allow workers to check schedules, pickup, and trade shifts with online self-service.
- Inform workers about schedule changes in real-time with automatic notifications.
- Build fairness and trust by balancing overtime distribution among employees.
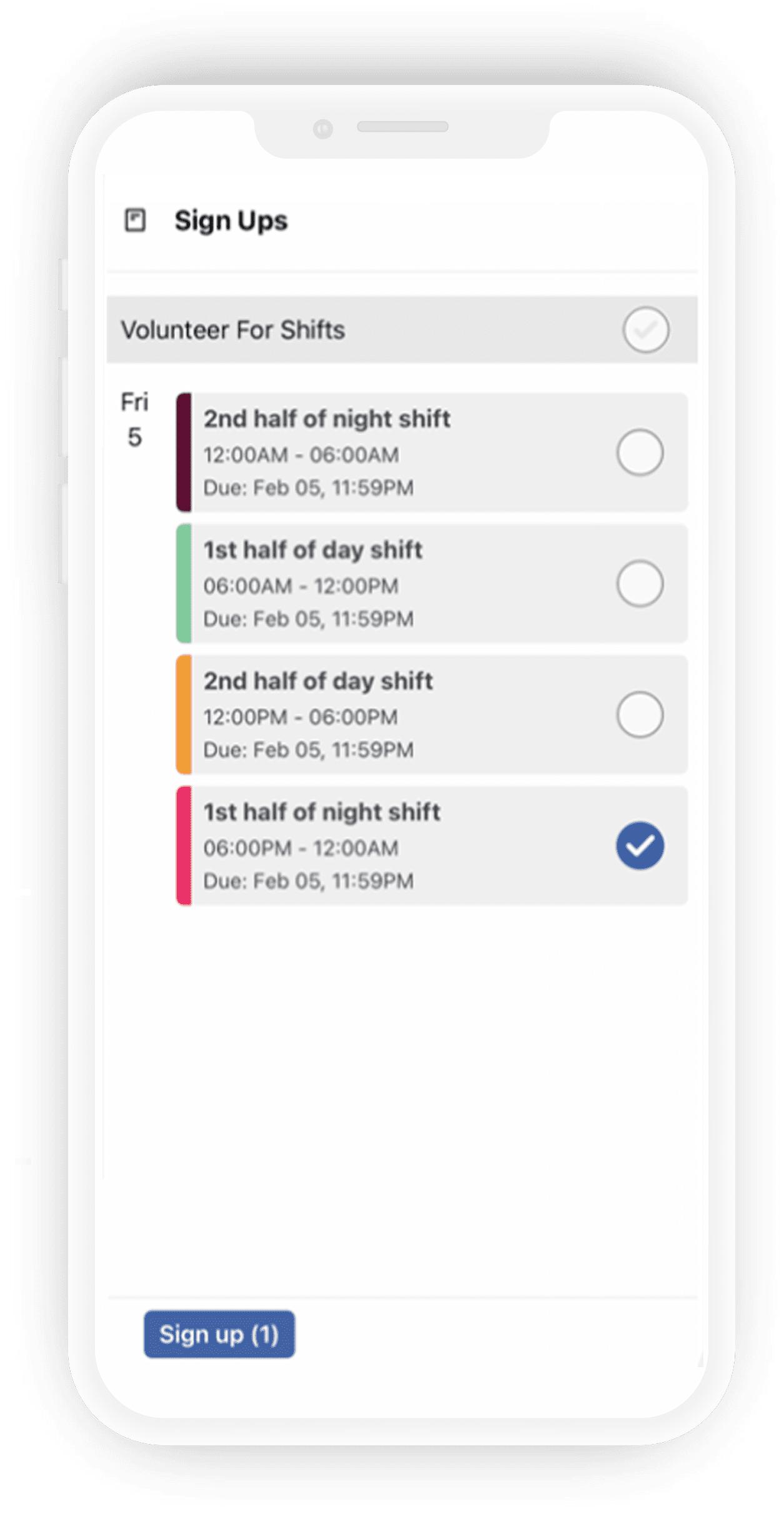
Lower Overtime and Labor Costs
Reduce overtime and overstaffing to drive higher cost-efficiency.
- Prioritize workers based on the least overtime cost implications.
- Uncover schedule moves to fill gaps before resorting to extra overtime and labor.
- Reassign underutilized workers and shuffle them to areas that need them the most.
- Gain clear visibility into current and forecast overtime stats to stay on budget.
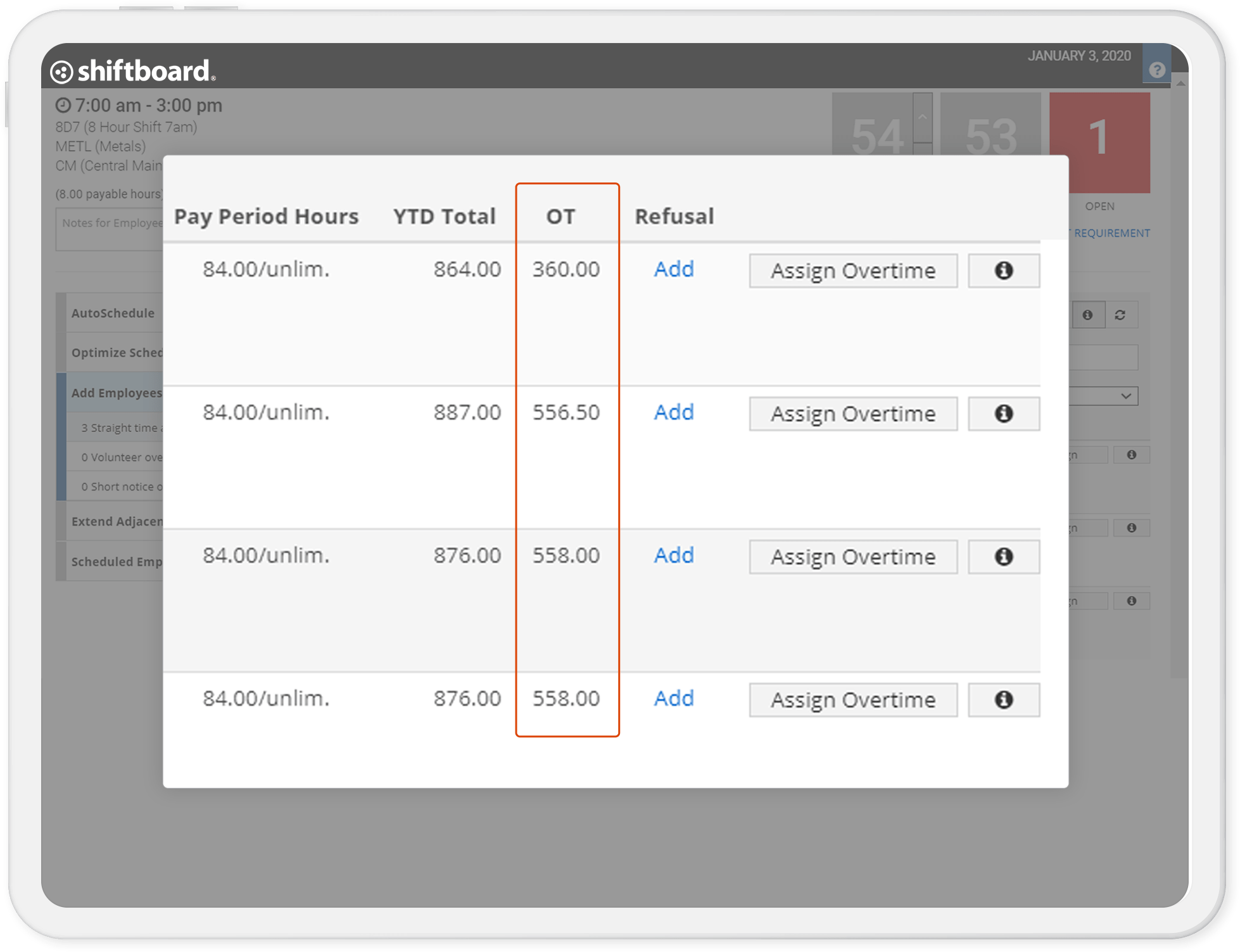
5 Reasons Manufacturers Choose Shiftboard
1.
Tailor-Fit Scheduling Automation
Match staffing to production schedules with automated scheduling processes configured to the way each plant and unit operates. Support manufacturing-specific scenarios such as production line changes, worker shuffles, and more.
2.
Worker-Friendly Schedules
Versatile toolsets to track and accommodate workers’ availability and shift preferences. Create schedules that different worker types embrace.
3.
Coverage Optimization and Agility
Unlock new coverage possibilities with intelligent scheduling suggestions powered by a robust, always-on optimization engine — purpose-built for operations with dynamic staffing demands and labor pool flexing needs.
4.
Overtime Equalization
Ensure fair hour assignments among employees with exclusive OT detection and equalization mechanisms.
5.
Full-Cycle Compliance
Go beyond rules enforcement and support exceptions management and audit logging. The only compliance guarantee available in the marketplace
Employee Scheduling for Manufacturing: A Best Practices Guide
Learn six best practices to develop an employee scheduling strategy to improve productivity and reduce costs.
Shiftboard for Manufacturing Solution Sheet
Learn more about how Shiftboard’s solutions can help you lower costs, increase efficiency, and improve safety.
“Shiftboard has helped our employees get more visibility into their work schedules and make changes on the go. It is easy to use and has given more structure to our scheduling process.”
Tyler Blake, Senior HR Generalist, Daisy Brand
More Manufacturing Industry Insights
Want to learn more about employee scheduling software?
Decrease Worker
Turnover by 16%
Make Scheduling
30% More Efficient
Increase Shift Coverage
Rates by 88%
Frequently Asked Questions
These are some questions we frequently hear from people looking for workforce management software for manufacturing.
-
Why Shiftboard for employee scheduling in manufacturing?
Shiftboard is purpose-built to ease the complexity of managing manufacturing work schedules. Its technology is highly configurable to match the specific needs of each plant or unit, ensuring that every shift is optimized for maximum coverage cost effectiveness, and employee satisfaction.
-
Why is effective employee communication important to operational success?
Effective worker communication is the kingpin of strong worker engagement. For operations, timely and rapid response to staffing demand changes requires full worker cooperation. Keeping workers informed of operational changes can help reduce avoidable absences, tardiness, and scheduling conflicts. Keeping workers informed – in real-time – can help them plan their lives outside work and ultimately improves worker satisfaction and retention.
-
What is demand-based scheduling?
Demand-based scheduling is the process of aligning employee schedules to production plans on any given day. Manufacturing shift scheduling software may be used to help managers visualize which lines are running and where coverage gaps may occur. Armed with this real-time view, schedulers can quickly assess, reassign, and shuffle workers to rebalance lines as production and labor changes occur.
-
How do you optimize the employee schedule for cost-effectiveness?
Managers can control labor costs better by gaining visibility into the cost implications related to employee shift assignments. Assigning shifts based on workforce data, such as workers’ base pay rates, overtime status, recent work history, or other pay rate triggers, helps managers schedule the most cost-effective, qualified workers for each role. Leveraging labor cost insights during the scheduling process is an excellent way to reduce wasteful overtime, avoid overstaffing, and create an optimized schedule.